Understanding the Art of Welding: Just How to Avoid Undercut Welding Issues for Flawless Fabrication Results
By recognizing the root triggers of undercut welding and executing reliable methods to avoid it, welders can raise their craft to new degrees of excellence. In the pursuit of remarkable manufacture results, mastering the art of welding to stay clear of undercut problems is not just an ability however a necessity for those making every effort for excellence in their work.
Recognizing Undercut Welding

To avoid undercut welding, welders must make certain correct welding parameters, such as adjusting the present, voltage, travel speed, and preserving the proper electrode angle. By understanding the causes of undercut welding and implementing preventive steps, welders can achieve premium, structurally sound welds.
Causes of Undercut in Welding
Understanding the variables that contribute to undercut in welding is vital for welders to produce high-grade, structurally sound welds. Poor welding present or wrong welding rate can additionally add to undercut. Understanding these reasons and executing appropriate welding methods can assist protect against damaging issues, making sure sturdy and solid welds.
Methods to stop Undercutting

To mitigate the threat of damaging in welding, welders can use tactical welding strategies aimed at boosting the quality and honesty of the weld joints. Furthermore, using the correct welding strategy for the details joint configuration, such as weave or stringer beads, can add to minimizing damaging.
In addition, appropriate joint prep work, consisting of making sure tidy base products without impurities and making use of the appropriate welding consumables, is important in protecting against undercut problems. Employing back-step welding methods and controlling the weld bead profile can also aid disperse warm uniformly and minimize the threat of undercut. Regular evaluation of the weld joint throughout and after welding, along with carrying out high quality assurance actions, can assist in addressing and discovering damaging concerns quickly. By implementing these methods faithfully, welders can attain perfect fabrication results with marginal undercut flaws.
Significance of Correct Welding Criteria
Picking and preserving suitable welding specifications is essential for achieving successful welds with minimal problems. Welding criteria describe variables such as voltage, current, take a trip rate, electrode angle, and protecting gas flow rate that directly influence the welding procedure. These criteria have to be carefully readjusted based upon the type of material being bonded, its density, and the welding method employed.
Proper welding criteria make certain the correct amount of heat is put on thaw the base metals and filler material evenly. If the parameters are established expensive, it can result in excessive warmth input, creating spatter, distortion, or burn-through. On the various other hand, if the criteria are as well low, insufficient combination, lack of infiltration, or damaging may occur.
Quality Control in Welding Workflow
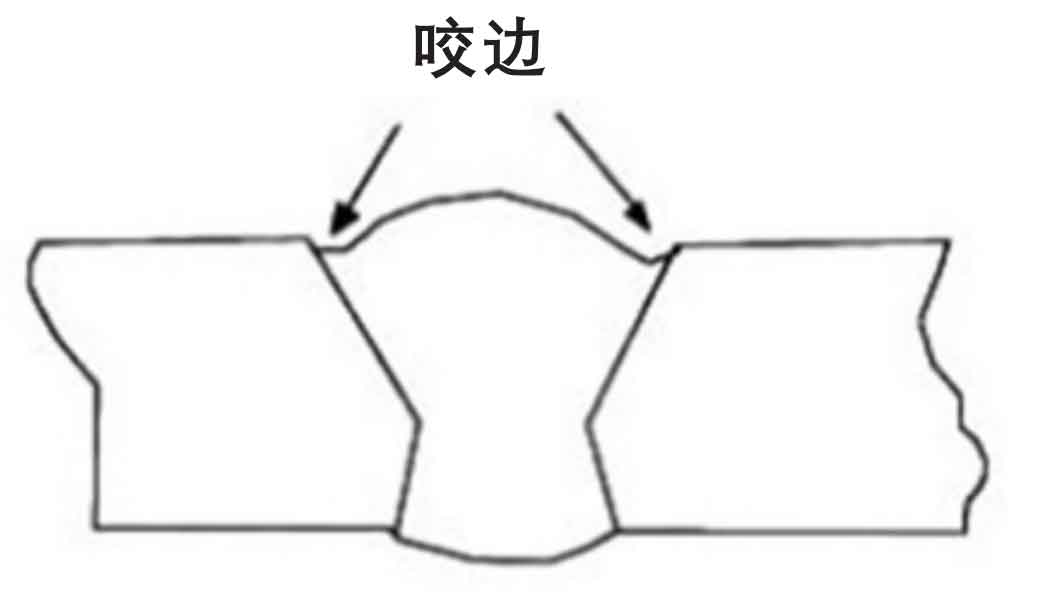
Conclusion
In conclusion, grasping the art of welding needs a complete understanding of undercut welding, its reasons, and strategies to stop it. By guaranteeing correct welding parameters and implementing quality control practices, flawless construction results can be attained. It is crucial for welders to continually aim for excellence in their welding procedures to prevent undercut issues and produce high-grade welds.
Undercut welding, a typical problem in welding procedures, happens when the weld metal does not correctly fill the groove and leaves a groove or clinical depression along the welded Full Article joint.To protect against undercut welding, welders must guarantee correct welding specifications, such as adjusting the existing, voltage, travel rate, and maintaining the right electrode angle. Inadequate welding existing or incorrect welding rate can also contribute to damage.To reduce the threat of undercutting in welding, welders can use tactical welding methods intended at improving the top quality and integrity of the weld joints.In final thought, mastering the art of welding needs an extensive understanding additional reading of undercut welding, its reasons, and techniques to avoid it.